Why Regular Packaging Machine Repair Is Essential for Your Business
Why Regular Packaging Machine Repair Is Essential for Your Business
Blog Article
The Ultimate Overview to Product Packaging Machine Repair Work: Keep Your Procedures Running Efficiently
In the world of packaging, the performance of procedures pivots significantly on the dependability of machinery. Comprehending the details of product packaging equipment repair is crucial for maintaining optimum efficiency and minimizing disturbances. Routine upkeep not only expands the life of these machines yet additionally addresses common issues that can hamper productivity. As we discover the subtleties of troubleshooting and the vital decision-making process between repair service and replacement, it ends up being clear that a proactive technique can generate substantial benefits. What particular techniques can companies apply to ensure their packaging operations remain uninterrupted?
Significance of Normal Upkeep
Normal upkeep of product packaging equipments is vital for ensuring ideal performance and long life. By executing a structured upkeep schedule, operators can recognize prospective concerns before they rise into substantial problems. This aggressive method not just reduces downtime yet also expands the lifespan of the tools, ultimately bring about decreased functional costs.
Routine inspections enable for the assessment of essential parts such as belts, seals, and sensing units. Addressing deterioration without delay avoids unforeseen failings that might interfere with production and result in expensive fixings. Additionally, regular upkeep aids ensure conformity with sector standards and policies, cultivating a secure working environment.
Furthermore, upkeep tasks such as cleaning, lubrication, and calibration dramatically boost machine efficiency. Improved performance equates to regular item quality, which is important for preserving client contentment and brand name online reputation. A well-maintained packaging maker runs at ideal speeds and minimizes material waste, contributing to overall efficiency.
Usual Packaging Equipment Concerns
Product packaging equipments, like any kind of intricate equipment, can experience a range of typical issues that may hinder their efficiency and performance - packaging machine repair. One common issue is inconsistent securing, which can result in item wasting and waste if packages are not properly secured. This usually arises from misaligned elements or worn securing aspects
One more frequent concern is mechanical jams, which can happen due to international things, worn components, or incorrect alignment. Jams can cause hold-ups in production and increase downtime, inevitably impacting overall performance. Furthermore, digital malfunctions, such as failure in sensing units or control systems, can interrupt procedures and lead to imprecise measurements or irregular maker behavior.
In addition, problems with item feed can additionally emerge, where products might not be provided to the product packaging area continually, triggering interruptions. Finally, wear and tear on rollers and belts can cause suboptimal efficiency, needing prompt attention to protect against further damages.
Recognizing these common problems is vital for keeping the integrity of packaging procedures, guaranteeing that equipment runs efficiently and efficiently, which consequently assists in conference production targets and maintaining product top quality.

Fixing Techniques
Reliable fixing techniques are essential for without delay resolving problems that occur with packaging makers. A methodical approach is essential for determining the origin cause of malfunctions and lessening downtime. Begin by gathering details concerning the signs observed; this may consist of unusual sounds, operational hold-ups, or error codes shown on the machine's user interface.
Next, describe the maker's manual for repairing guidelines certain to the model concerned. This resource can offer useful insights into usual issues and advised diagnostic steps. Make use of visual assessments to check for loose links, worn belts, or misaligned elements, as these physical variables frequently add to functional failures.
Carry out a procedure of elimination by testing specific machine functions. For example, if a seal is not creating correctly, examine the securing device and temperature settings to figure out if they fulfill operational specifications. File each step taken and the results observed, as this can help in future fixing initiatives.
Fixing vs. Replacement Choices
When confronted with equipment breakdowns, choosing whether to repair or replace a packaging maker can be a facility and essential selection. This choice depends upon a number of essential elements, including the age of the device, the degree of the damage, and the projected influence on functional effectiveness.
To start with, consider the equipment's age. Older makers may call for more constant repair work, leading to greater advancing prices that can exceed the financial investment in a new system.
Operational downtime is one more crucial consideration. Investing in a new equipment that provides improved performance and reliability may be more prudent if fixing the device will his comment is here certainly create prolonged delays. In addition, consider the accessibility of components; if substitute components are hard to find by, it might be extra tactical to replace the maker totally.
Ultimately, carrying out a cost-benefit analysis that consists of both lasting and prompt effects will certainly assist in making an informed decision that aligns with your operational goals and budgetary restrictions. (packaging machine repair)
Safety Nets for Durability
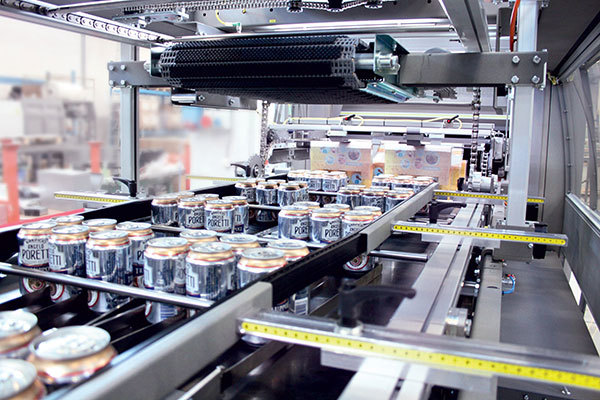
Key preventative actions include regular lubrication of moving parts, alignment checks, and calibration of sensors and controls. Developing a cleansing schedule to remove debris and pollutants from machinery can considerably minimize deterioration (packaging machine repair). Furthermore, keeping an eye on functional parameters such as temperature and vibration can aid spot irregularities early
Training personnel to recognize indicators of wear or breakdown is another important element of preventive maintenance. Equipping drivers with the understanding to execute fundamental troubleshooting can lead to quicker resolutions and lessen operational interruptions.
Documentation of upkeep tasks, including service documents and examination searchings for, fosters responsibility and facilitates informed decision-making regarding substitutes and repair services. By focusing on safety nets, organizations can ensure their product packaging devices operate at peak efficiency, inevitably causing boosted performance and lowered functional costs.
Verdict
To conclude, the efficient maintenance and fixing of product packaging devices are paramount for sustaining functional effectiveness. Routine maintenance minimizes the danger of common concerns, such as inconsistent securing and mechanical jams, while methodical troubleshooting strategies help with timely resolution of malfunctions. In addition, careful consideration of repair work versus substitute choices adds to cost-efficient management of resources. By carrying out preventative actions, companies can improve discover here maker long life and ensure undisturbed performance in packaging procedures.
Comprehending the complexities of packaging maker repair service is important for keeping ideal performance and lessening site link disruptions.Normal upkeep of product packaging machines is essential for guaranteeing ideal performance and longevity.Packaging machines, like any kind of complex machinery, can experience a variety of usual concerns that might prevent their efficiency and performance. If fixing the device will certainly create long term delays, spending in a new maker that offers enhanced performance and dependability might be much more sensible.In conclusion, the efficient maintenance and fixing of product packaging makers are vital for sustaining functional performance.
Report this page